Cell layout and reachability test
Which robot do you need for your palletizing station? And where do you place the pallet(s) and the robot? How do you ensure the robot is able to reach all pallet positions?
In this step, you will learn best practices of cell layout to enable you to create a first draft of your own palletizing station.
You will also learn how to perform a reachability test in a simulation tool to verify that the robot can reach all layers and positions on the pallet, and that the robot doesn't collide with any objects. The reachability test also helps you determine which kind of gripper you need, and whether you need a 7th axis.
- Create first draft of palletizing station
- Perform reachability test to verify the robot can reach all layers and positions
Downloads
Modules
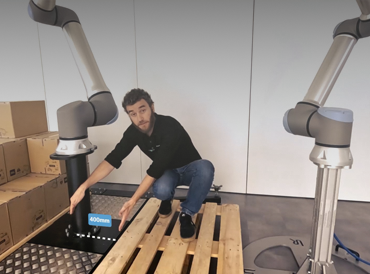
0.1. Cell layout best practices
- Layout design
- Pallet positioning
- Robot mounting
- Gripper mounting
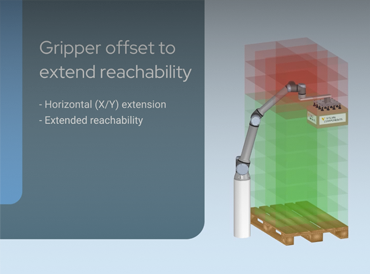
0.2. The theory of reachability test
- Reachability of all positions
- Detecting collisions
- Need of 7th axis
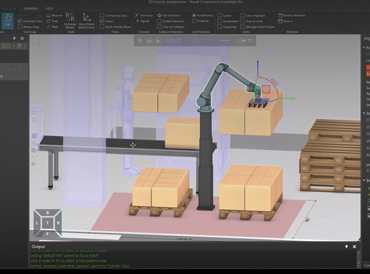
0.3. Customer Case - part 2: cell layout and reachability test
- 3D cell layout
- Reachability test
- Gripper design and mounting
Additional Resources
Goals check
Verify if you reached all the goals for this stage and you have everything you need to proceed.
Next stage:
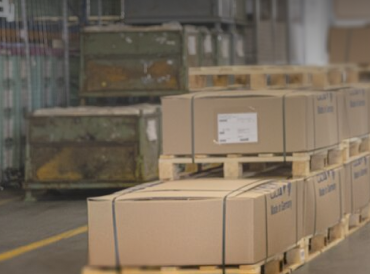
1. Documenting your existing process
The first steps towards automating your palletizing process is knowing all the ins and outs of it. The Palletizing Evaluation Tool provided in this step helps you document all the relevant aspects of your process that you will need when planning your project. The tool also provides you with a report that points out potential friction points in your process and gives recommendations on how to remove or reduce these friction points.
When you have completed this step, you will have a clear idea of the complexity of your project. You will know potential friction points in your process and how to reduce them.